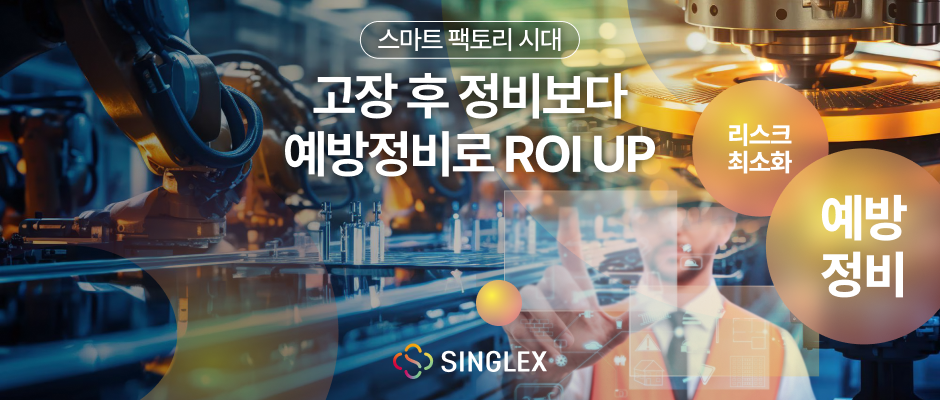
공장 가동 중단으로 인한 피해 비용 급증!
‘H사, 뜻밖의 설비 고장…”2주 가동 중단’, ‘D사 이물질 구리… 주조 설비 고장으로 가동 중단’, ‘S그룹 인명 사고, 사고 후 설비 가동이 원인?’ 등 공장 가동 중단과 관련된 최근 뉴스 헤드라인들입니다. 이처럼 뉴스로도 종종 접하는 설비 고장으로 인한 가동 중단의 피해는 예상보다 훨씬 심각합니다.

기술 기업 지멘스의 “The True Cost of Downtime” 보고서에 따르면, 공장의 업종별 1시간 가동 중단에 따른 손실 비용은 적게는 FMCG(소비재) 공장의 3만 9천 달러(약 5천만 원)부터, 많게는 자동차 공장의 200만 달러(약 263억 원)까지 발생할 수 있는데요. 특히 대형 공장 평균 가동 중단 비용은 연간 1억 2,900만 달러(약 170억 원)로, 2020년 조사 결과 대비 2022년에 65% 증가했습니다.
포춘 500대 기업(미국 경제지 포춘이 선정하는 글로벌 기업 리스트)들은 연간 1조 5천억 달러(약 19조 7천억 원)가량의 손실을 입는 것으로 추정되고 있는데요. 이는 해당 기업들의 매출 중 약 11%를 차지할 정도로 높은 금액입니다.
문제는 여기서 그치지 않습니다. 금액 등으로 정확히 표시되지 않는 무형 손실의 경우, 정확한 가동 중단 비용을 계산할 수 없기 때문인데요. 생산 중단으로 인한 직접적인 손실 외에도 제품 공급 지연으로 인한 고객 불만, 시장 점유율 감소, 브랜드 신뢰도 저하 등으로 인한 손실까지 고려하면 피해는 훨씬 더 커지게 됩니다. 특히 안전사고가 발생한다면, 무형의 피해가 더 심각해질 수 있습니다.
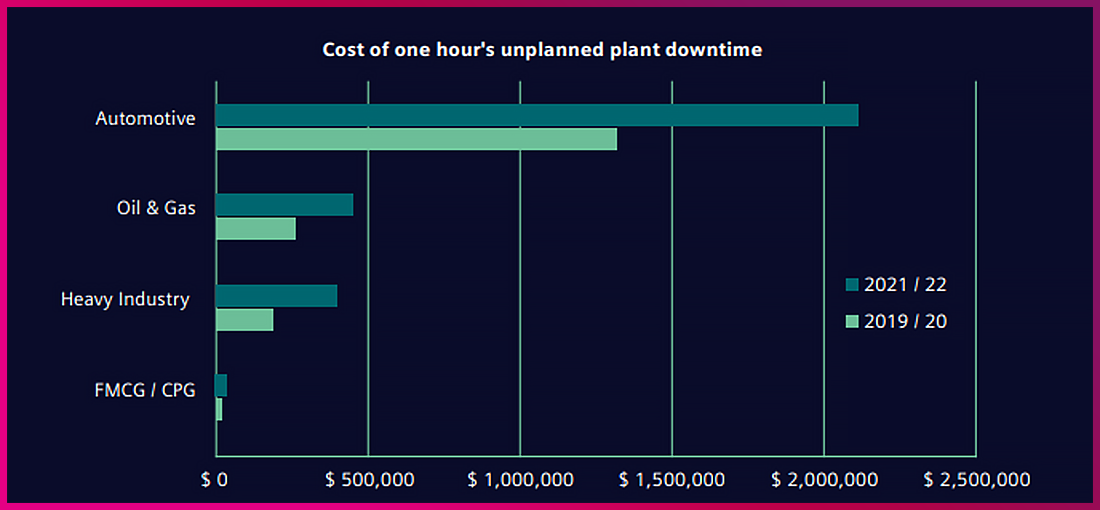
스마트팩토리 시대와 인력 부족
인더스트리 4.0(제조업과 같은 전통 산업에 IT시스템을 결합해 지능형 생산 시스템을 갖춘 스마트팩토리로 진화시키자는 산업 관련 정책) 시대에는 생산 속도가 획기적으로 높아졌지만 동시에 생산 시스템의 복잡성도 증가했습니다. 이는 상호 연결된 시스템으로 제조 공정이 작동하는 만큼 ‘단순한 기계 고장에도 기하급수적으로 더 큰 피해가 발생할 수 있다’는 의미이기도 합니다. 특히 스마트팩토리는 시스템간 상호 연결이 중요하기 때문에 한 기계의 작동 중단이 전체 생산에 영향을 미쳐 막대한 손실을 초래할 수도 있습니다.
‘숙련된 인력 부족’ 문제는 이와 같은 위험을 더욱 악화시킬 수 있는데요. 고용노동부 발표에 따르면, 2030년까지 15~64세 생산가능 인구는 약 320만 명 감소할 것으로 예측되며, 인구 고령화와 함께 제조업 분야의 숙련된 노동자가 더 빠르게 감소할 것으로 전망되고 있습니다. 금형, 용접, 조선, 도장 등 제조 현장 전반에 걸친 숙련공 부족 문제는 이미 제조업 전반에 걸쳐 심화되고 있으며, 이는 제조 및 생산 공장의 설비 고장 시 조치 상황에 여러가지 문제를 초래할 수 있습니다. 예를 들어, 설비의 고장 원인을 진단하고 해결하는 데 오랜 시간을 소요해 생산 중단 시간이 과도하게 증가할 수 있고, 설비 및 유지보수에 필요한 기술적 역량 확보 자체가 어려워져 국내 스마트팩토리 분야의 경쟁력을 약화하고 위험 요소를 더욱 심화 시킬 수 있습니다.
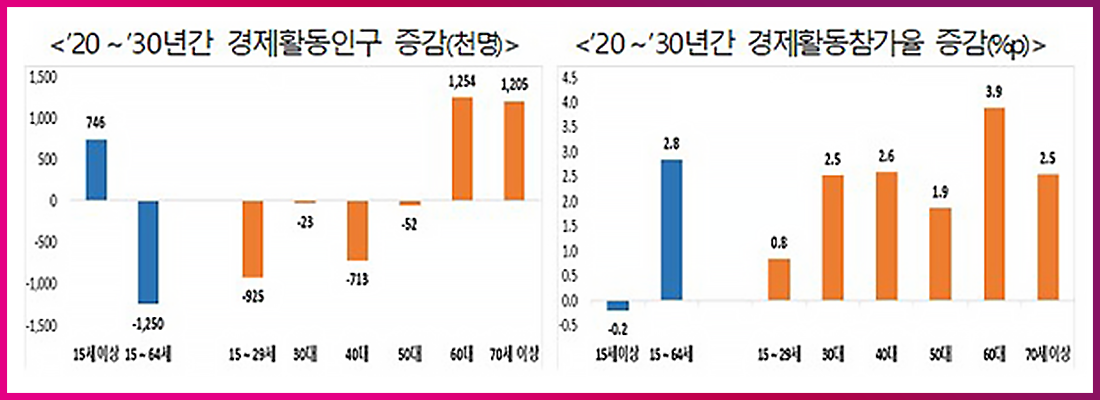
스마트팩토리 시대, 숙련된 인력 부족이 초래할 위기를 해결할 방법은 체계적인 설비관리 시스템을 구축하는 것입니다. 숙련된 인력이 갖고 있는 설비관리에 관한 지식과 경험을 체계적으로 표준화하고 데이터베이스화해 신규 인력이 쉽게 정비 지식을 습득하고, 실무에 적용할 수 있도록 해야 합니다. 또한 설비 고장 사전 예방과 문제 발생 시 신속한 해결을 지원하는 설비관리 시스템 구축 역시 필요합니다.
공장 설비 정비의 두 가지 방법
• 예방 정비(PM)와 고장 정비(BM)
예방 정비는 고장을 사전에 방지하고, 설비를 항상 최적의 상태로 유지하기 위해 정기적으로 검사하고 관리하는 것을 의미합니다. 즉, 정기적인 자동차 엔진 오일 교체와 타이어 검사처럼 설비의 부품 상태를 점검하고, 필요한 조치를 주기적으로 취해 고장 발생 가능성을 낮추는 것입니다. 반면 고장 정비는 이미 발생한 설비 고장을 진단하고 해결하는 것을 의미합니다.
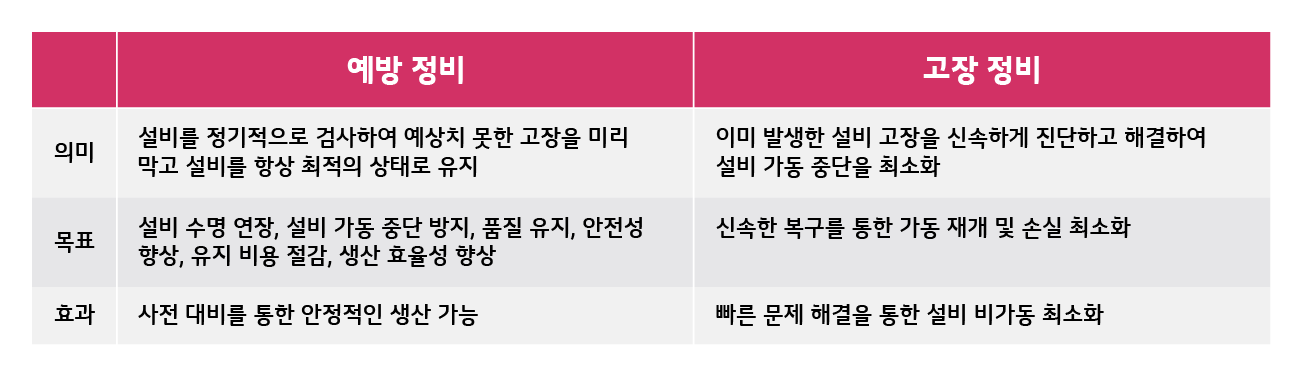
현대 제조 환경에서 예방 정비는 필수 전략으로 자리 잡았습니다. 실제로 예방 정비는 투자 수익률(ROI) 측면에서도 긍정적인 효과를 보여주는데요. 글로벌 리서치 및 컨설팅 기업 포레스터 컨설팅의 연구에 따르면, 한 예방적 유지보수 솔루션은 202%의 높은 투자 수익률을 달성했고, 부동산 서비스 기업 Jones Lang LaSalle는 예방적 유지보수 프로세스 도입으로 ROI 545%라는 놀라운 결과를 달성한 바 있습니다.
예방 정비가 높은 ROI를 제공하는 이유는 다음과 같은 효과들 덕분입니다.
• 장비 성능 향상 및 수명 연장 : 예방 정비를 통해 장비 상태를 지속적으로 모니터링하고 필요한 조치를 취함으로써, 장비의 최적 성능을 유지하고 수명을 연장할 수 있습니다. 이는 생산성 향상과 유지 관리 비용 절감으로 이어집니다.
• 안전성 향상 : 예방 정비는 장비 고장을 방지해 작업자의 안전을 확보하고 작업 환경을 개선하는 데 기여합니다. 또한, 사고 예방으로 인해 발생하는 손실을 줄일 수 있습니다.
• 다운타임 감소 : 예방 정비를 통해 장비 고장을 사전에 예측하고 예방 조치를 취함으로써 다운타임을 최소화할 수 있습니다. 이는 생산 손실을 줄이고 생산 일정을 준수하는 데 도움이 됩니다.
• 생산 효율성 향상 : 예방 정비를 통해 장비의 최적 성능을 유지하고 예기치 않은 다운타임을 감소시킴으로써 생산 효율성을 크게 향상시킬 수 있습니다.
설비관리 유/무형 비용 ROI 극대화는? SINGLEX와 함께!
SINGLEX 설비관리를 통한 예방 정비로 장비 수명 연장, 예기치 않은 가동 중단 감소, 생산 효율성 향상을 이끌어 유지 관리 비용, 생산 손실 비용, 안전사고 비용 등을 크게 절감할 수 있습니다. 정밀 기계와 자동화 시스템이 생산의 핵심을 이루는 스마트팩토리 시대에는 예방 정비의 중요성이 더욱 강조됩니다.
‘예방 정비’란 일정한 주기로 설비 상태를 점검하고 필요 시 교환이나 수리를 진행하는 정비 방법으로, 고장을 예방하기 위한 정비 방법과 절차를 미리 정의해 예방 정비 절차를 표준화 하는 것이 필수입니다.
예방 정비 작업 절차를 좀 더 자세히 살펴보겠습니다. 예방 정비 작업 항목(PM OP, PM Operation)은 작업 명, 작업 상세 방법, 작업에 필요한 작업 인원수, 소요 시간, 필요 설비 자재와 소요량, 점검 항복, 주기 등으로 구성됩니다. 예방 정비 작업 항목(PM OP)을 순서대로 연결하면 예방 정비 작업 절차(PM Activity)가 구성됩니다. 이때 각 작업 항목 간(OP)의 연관성과 작업 간의 로직을 명확하게 정의하는 것이 중요합니다. 특정 설비의 예방 정비 작업을 준비하기 위해서는 정비 전문가의 Know-How를 바탕으로 예방 정비 작업 항목과 예방 정비 작업 절차를 미리 작성해야 합니다. 이 과정을 포함한 전체 프로세스는 [그림 3]과 같습니다.
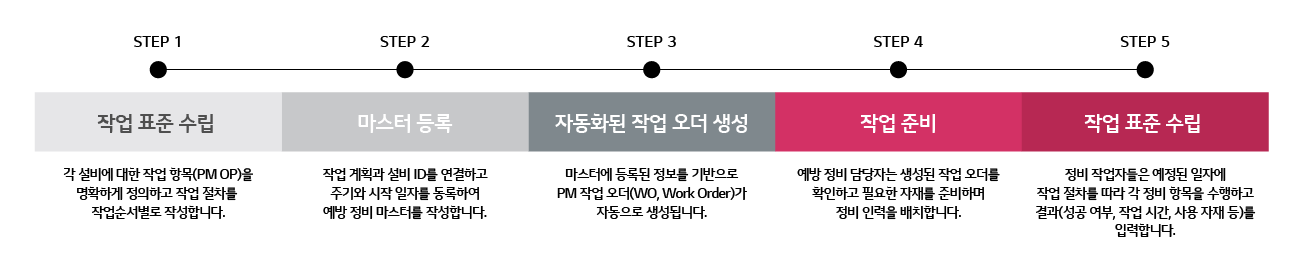
STEP1. 작업 표준 수립 : 각 설비에 대한 PM OP를 명확하게 정의하고 PM Activity를 작업순서 별로 작성합니다.
STEP2. 마스터 등록 : 작업 계획과 설비 ID를 연결하고 주기와 시작 일자를 등록해 예방 정비 마스터를 작성합니다.
STEP3. 자동화된 작업 오더 생성 : 마스터에 등록된 정보를 기반으로 PM 작업 오더(WO, Work Order)가 자동으로 생성됩니다.
STEP4. 작업 준비 : 예방 정비 담당자는 생성된 작업 오더를 확인하고 필요한 자재를 준비하며 정비 인력을 배치합니다.
STEP5. 작업 수행 : 정비 작업자들은 예정된 일자에 작업 절차를 따라 각 정비 항목을 수행하고 결과(성공 여부, 작업 시간, 사용 자재 등)를 입력합니다.
설비관리 시스템 도입이 필요하다면?
예방정비는 스마트팩토리의 생산성, 안전성, 경쟁력을 확보하기 위해서 필수입니다. SINGLEX 설비관리(EMS) 서비스는 글로벌 수준의 체계적인 시스템으로, 예방 정비와 고장 정비를 모두 지원하며 도입 시 다음과 같은 효과를 누릴 수 있습니다.
• 정비 지식 표준화 및 데이터베이스 구축 : 숙련공들의 노하우를 체계적으로 관리하고 쉽게 활용할 수 있도록 지원합니다.
• 예방 정비 체계 구축 : 예방 정비가 가능한 시스템과 가이드, 매뉴얼 등을 제공합니다. 이를 통해 설비 고장을 사전에 예방해 생산 중단을 줄이고 안정적인 생산을 유지합니다.
• 고장 정비 체계 구축 : 설비 고장 발생 시 신속하게 진단하고 해결할 수 있도록 고장현장/점검/원인/조치에 대한 가이드를 제공해 생산 중단 시간을 최소화합니다.
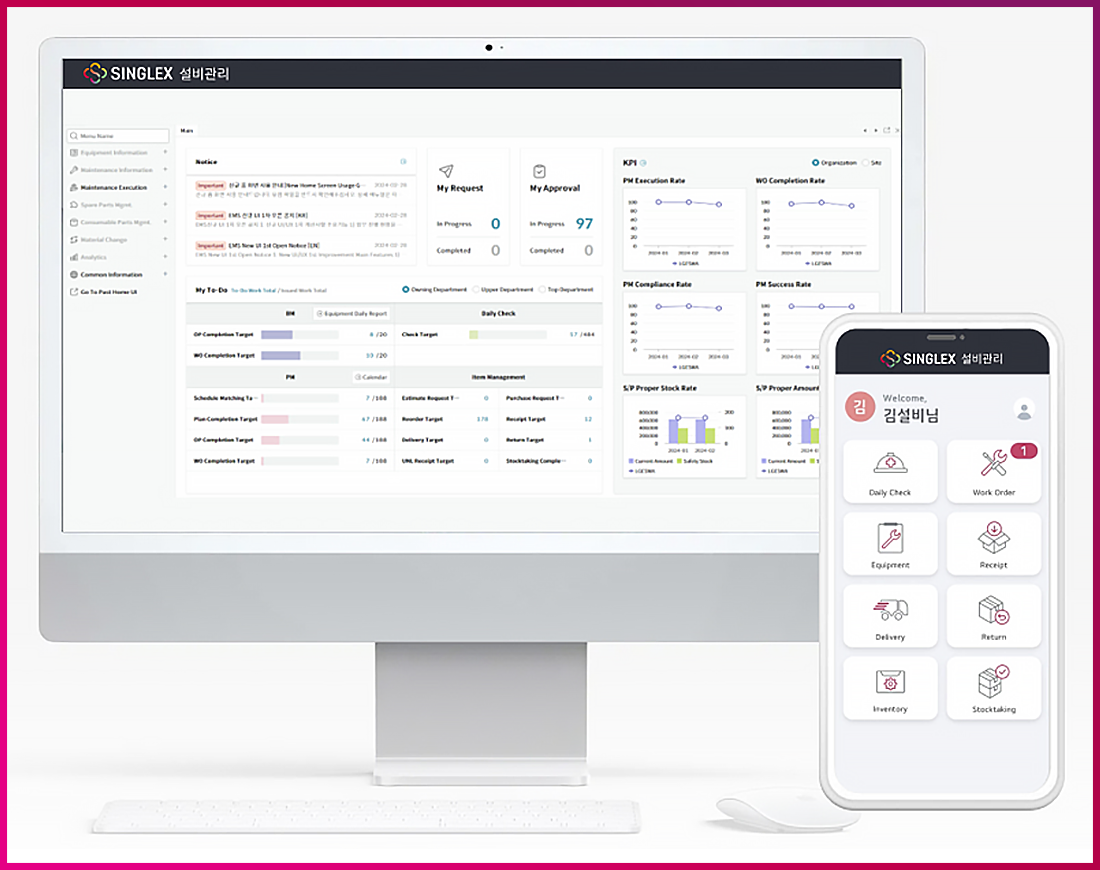
SINGLEX 설비관리(EMS)는 LG의 오랜 제조 생산 노하우와 전문성, 다양한 산업 분야의 설비 관련 경험을 바탕으로 최적화된 솔루션을 제공해 고객사의 효과적인 설비관리를 지원합니다. 더 나아가, 빅데이터와 AI 기술을 활용한 예지 정비(PdM, Predictive Maintenance) 솔루션을 결합해 더 발전된 설비관리 시스템으로 스마트팩토리의 미래를 함께 열어갈 계획입니다.
글ㅣLG CNS Business Process Innovation팀 김상태 총괄