물류센터 구축을 위해 과거에는 기계 관련 학문을 전공한 엔지니어가 제도판에서 도면을 그리고 설계를 완성해 나갔다면 이제는 해당 학과 전공자 이거나 전문가가 아니어도 자동화 물류센터의 설계를 데이터와 알고리즘 기반으로 할 수 있게 되었습니다.
예를 들어, 설계 소프트웨어를 사용해 센터 대상 건물의 사이즈와 요구 물동량을 입력하면 보관량과 자동화를 위한 로봇의 대수가 자동으로 산정되며 바로 레이아웃을 2D, 3D로 작성하고 실제 요구 물동량에 맞게 입고, 출고되는지를 시뮬레이션해 볼 수 있습니다. (그림 1)
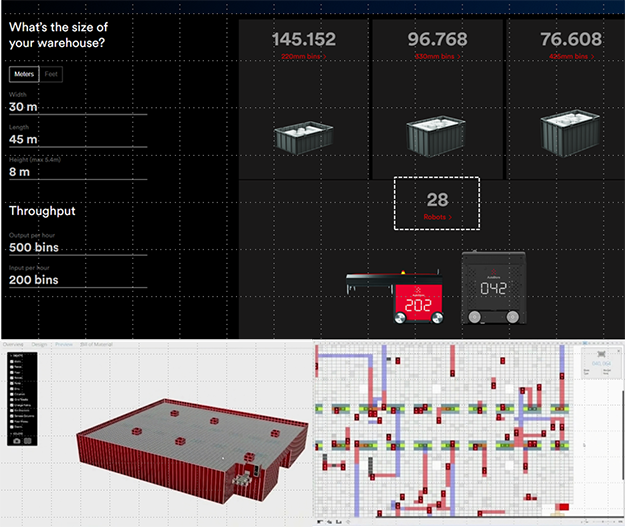
이렇듯 IT 기술 발달로 인한 물류센터 설계의 단적인 변화뿐만 아니라 더 빠르게 다양한 상품과 서비스를 요구하는 소비자 요구에 따라 물류는 기업의 성패를 가르는 핵심 경쟁요소가 되고 있으며, 이러한 시대와 환경 변화에 가치를 담기 위해 물류센터는 지속적인 혁신이 필요하게 되었습니다.
4차 산업혁명과 온라인, 아마존으로부터 촉발된 물류 산업 전반에 걸쳐 진행 중인 변화 안에서 살아남기 위해서는 끊임없이 혁신해야 하고 이에 기존 방식에 대한 의문을 제기하고 사업의 불확실성, 투자 패러다임의 변화, 플랫폼 사업자의 혁신 가속화, 기술과 환경의 변화 속도를 고려한 공간, 생산성, 기술에 대한 물류 측면에서의 새로운 정의를 내려보고자 합니다.
공간에 대한 재정의
먼저 공간에 대한 재정의입니다. 사업과 환경 변화에 레고 블록처럼 유연하게 물류센터가 대응할 수는 없을까요? 공간을 정적인 개념이 아닌 동적인 개념으로 보는 새로운 시각이 필요하며 공간은 더 고정되지 않고 상품과 고객에 따라 변화해야 합니다.
지금까지 물류센터를 설계하기 위해서는 사업 계획을 수립하고 전략 방향과 목표 물동량을 정의하고 부지를 확보하고 센터 내에 공간을 분류, 할당하고 작업 단위별 운영방식 정의에 따라 장비를 선정해 채워 나가는 방식이었습니다. (그림 2)
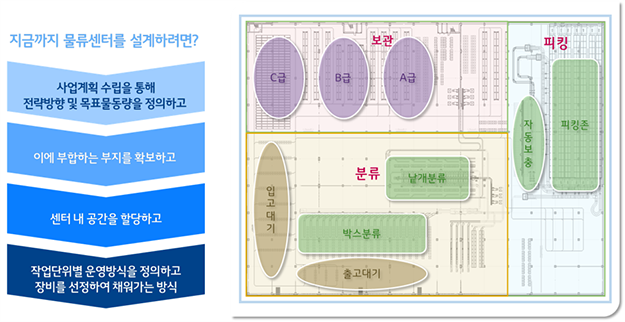
하지만 물류센터를 운영하던 중에 센터를 이동하거나 기능 변화가 생긴다면? 센터 규모와 역할이 달라지면? 품목별 출하 빈도가 변경되면? 계획했던 물동과 품목이 2배가 되면? 이러한 예측하지 못했던 다양한 변화에 지금까지의 방식대로 대응이 과연 가능할지 의문이 생기게 됩니다.
환경 변화에 대응을 넘어 고객을 위한 가치 창조와 혁신을 도모하는 유연한 센터 설계를 위한 “새로운 시각”이 필요하며 이에 세 가지 새로운 정의를 내려보고자 합니다.
첫 번째로 No more zone-based storage and picking(작업 공간에 대한 새로운 정의)입니다. 등급별로 보관 영역을 구분하고 상품을 이동, 관리할 필요 없이 사용에 따라 자연스럽게 등급별로, 상품별로 최적화되는 자율지능형 센터가 그 예입니다. (그림 3)
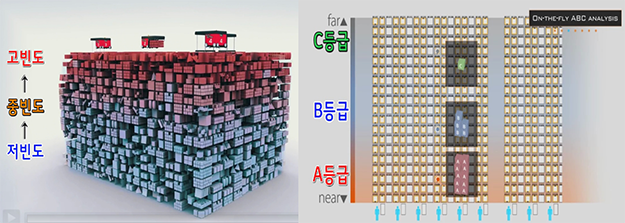
이러한 자율지능형 물류센터를 적용하면 센터 운영 상황에 따라 자동으로 상품의 배치가 등급별로 조정이 가능합니다.
두 번째로 No more usage of a cell for only one SKU(보관 방식에 대한 새로운 접근)입니다. 동일 상품을 동일 위치에 보관하지 않고 Random Stow 전략을 통해 보관 공간, 적치 시간 및 이동 시간을 최소화해 생산성 중심의 센터로 변화해야 하며 그 중심에는 AI, 최적화 알고리즘 등 IT 기술이 필수적입니다. (그림 4)
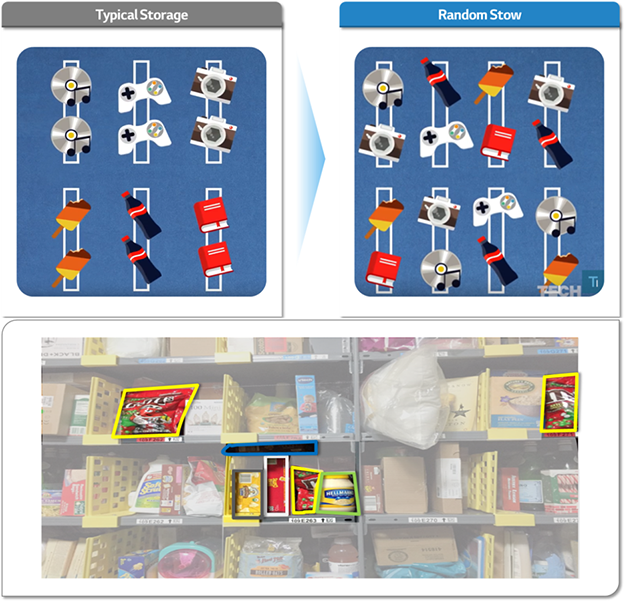
마지막으로 No more rigid Infrastructure(변화와 확장에 용이한 새로운 조합)입니다. 이를 위해 모듈화된 솔루션으로 물류센터의 유연성을 높여야 하며 어떠한 모양으로도 기둥 등 건물 내의 어떤 간섭도 방해가 되지 않고 이전으로 인한 재설치, 확장이 용이한 솔루션 적용이 필요합니다. (그림 5, 그림 6)
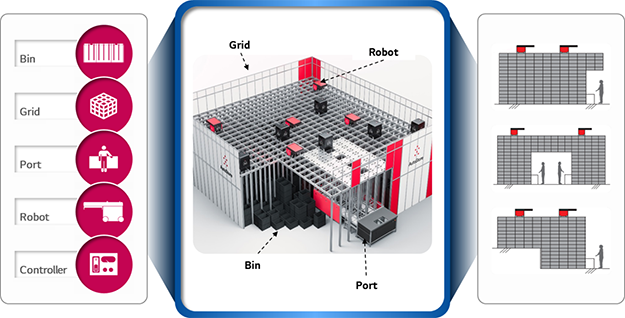
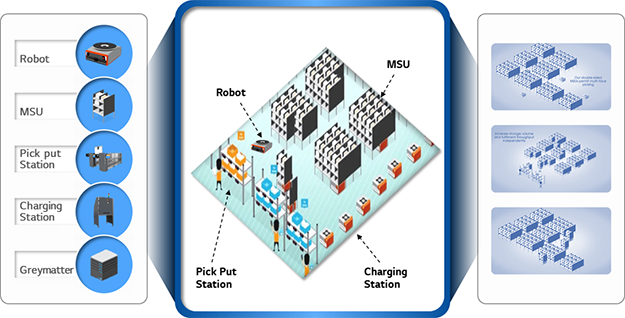
생산성에 대한 재정의
이어서 생산성 재정의에 대해 설명해보고자 합니다. 물류센터의 생산성은 언제까지 인력과 설비에만 의존해야 할까요?
숙련, 비숙련 혹은 야간, 주간 인력의 생산성 편차로 인한 비용 증가와 자동화된 물류센터가 오픈된 이후에 예상했던 설비의 능력과 운영 능력과의 차이, 설비 복잡도 증가로 인한 제어 난이도 증가로 인한 성능 저하, 오픈 후 감가에 따라 지속적으로 가치가 감소되는 현상을 고려해 보면 인력과 설비 중심의 물류센터는 새로운 정의가 필요합니다.
특히, 물류 현장에서는 생산성의 극대화, 인력 및 운영 비용의 최소화, 주문 출고율 향상, 작업 편의성 재고, 안정성 강화와 시스템의 유연성이 요구되고 있으며 이를 위해 인력, 설비 중심의 고려와 함께 데이터, 알고리즘 기반의 인간과 기계, 운영의 협업이 강화된 센터로의 접근을 시작해야 합니다.
지금까지 인력과 설비 중심의 단순 재고 증가 차감 계산, 설비 처리량 계산으로 생산성을 가늠했다면 데이터와 알고리즘을 기반으로 운영함으로써 하드웨어가 가지는 물리적인 한계를 소프트웨어로 극복하고 학습과 경험으로 누적된 데이터와 고도화된 알고리즘으로 생산성의 차원이 다른 센터 구축이 가능하게 됩니다. (그림 7)
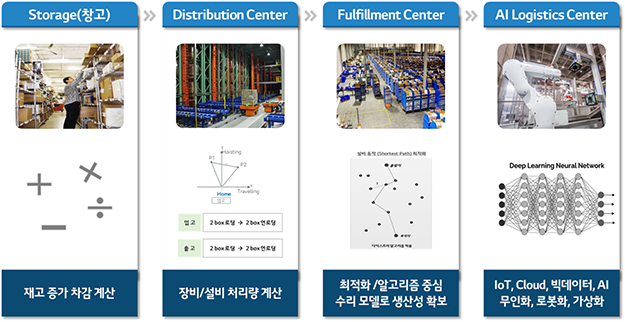
아울러 여러 다양한 설비의 조합이 고도화되고 심화되며 자동화가 요구되는 물류센터 발전 방향을 고려할 때 생산성의 극대화를 위한 WES(Warehouse Execution System)의 역할이 중요해지고 있습니다. WMS가 중앙관제 역할을 하는 대뇌, WCS가 다양한 신체 기능을 제어하는 뇌간, 척수의 역할이라면, WES는 운영 최적화를 지원하는 소프트웨어입니다. (그림 8)
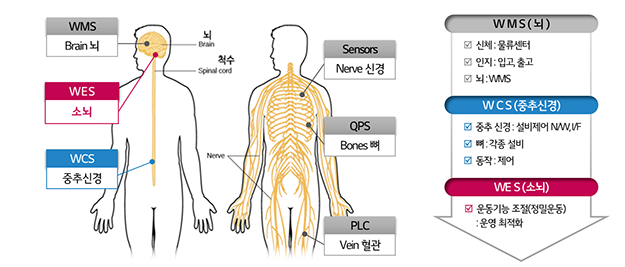
최적의 알고리즘 또한 생산성 극대화를 위한 핵심 사항이며 오더 처리, 작업 단위, 작업 부하 분산, 이동 물동량 최적화 등 물류센터 각 요소에 적용이 가능한 최적화 알고리즘을 통해 성능 향상은 물론 비용 절감까지 가능합니다. (그림 9)
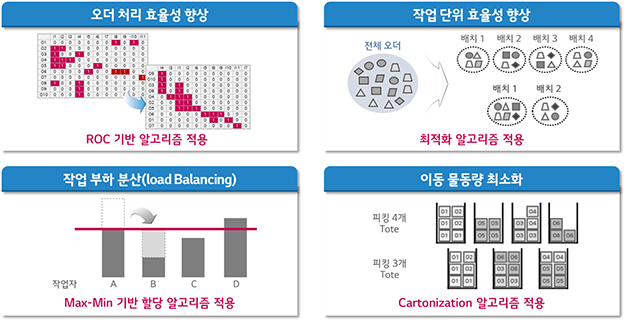
기술 측면에서의 재정의
공간, 생산성의 새로운 정의에 이어 기술 측면에서는 Industry 4.0의 핵심 디지털 기술과 유통, 비즈니스의 변화 속에 물류의 디지털화와 함께 물류 혁신의 트렌드가 가속화되고 있다고 볼 수 있습니다.
특히, IT 기술 발전으로 인한 리드 타임 단축, 생산성 극대화, 물류 비용 절감, 운영 편의성 증대 등 물류 서비스 가치의 변화로 이어지고 있습니다.
세계 3대 물류 산업 전시회인 Hannover Messe, Chicago ProMat, Logis-Tech Tokyo에서는 다양한 지능화 기술을 토대로 물류 산업의 Digitalization 가속화에 주목하고 있었으며 Artificial Intelligence, Predictive Maintenance, Digital Twin, Cobots 등이 핵심 키워드로 고려될 수 있었습니다.
이에 물류센터에 실행 가능한 기술을 중심으로 활발한 응용이 이루어지고 있으며 IoT와 디지털 트윈 기술의 센터 유지 보수 적용을 한 가지 예제로 설명할 수 있습니다.
센터 중단으로 인한 비용, 시간, 인력 소모를 최소화하면서 센터 생산성과 가동률을 동시에 향상시킬 수 있는 방법으로 IoT 기술을 활용한 고장 예측 모니터링 시스템 구축이 실제 적용되고 있으며, 특히 빅데이터 기술과 연계해 분석을 통한 설비 관리 시점 사전 알림이 가능합니다.
이상 징후 감지, 주요 부품의 잔여 수명 예측, 최적의 유지 보수 결정에 활용이 가능합니다. 기존 2D 스카다 기반의 센터 모니터링이 3D 기반의 디지털 트윈 기술 적용으로 현장 상황을 빠르게 파악하고 신속하게 대응할 수 있도록 할 수 있으며 IoT 기술 적용과 함께 선제적 장애 대응으로 센터의 생산성 및 가동률을 극대화할 수 있습니다. (그림 10)
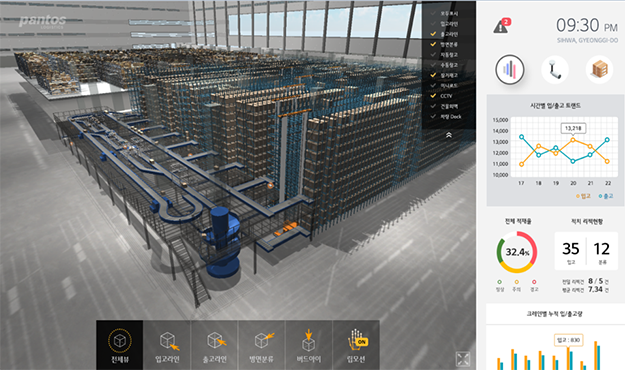
AI 기술의 적용도 물류센터에 활발히 이루어지고 있습니다. 택배 현장에서 인력에만 의존했던 상품 분류의 한계를 AI 기술을 활용해 개선한 사례를 보면, 택배 센터에서 기존 하차 이후에 인력으로 소형, 중대형, 이형으로 분류하던 방식에서 이미지 인식, 체적 분석, AI 기술 활용을 통한 지능형 화물 자동 분류를 적용해 해당 라인의 인력을 절감할 수 있습니다. (그림 11)
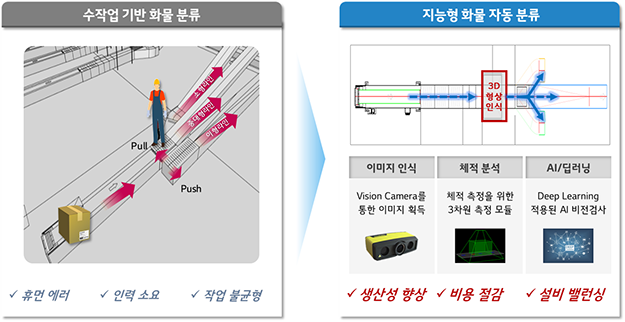
AI 기술 활용의 또 다른 예로 피킹로봇을 들 수 있습니다. 피킹로봇을 활용하면 생산성 향상과 24시간 365일 운영이 가능합니다.
또한 피킹로봇은 피킹 정확도 향상과 안정적인 화물 피킹을 위한 지속적인 AI, 딥러닝 적용이 반영되어 실제 물류센터에 적용이 가능한 단계로 진화하고 있습니다. (그림 12)
더불어 자동화 적용 수준이 상대적으로 미비한 하차, 상차, 적재, 검수와 포장 영역까지 전방위로 자동화가 확장되고 있습니다.
지금까지 물류센터의 지속적 혁신을 위한 공간, 생산성, 기술 측면의 새로운 정의를 설명했습니다. 결론으로 기술의 변화와 사업 환경의 급격한 변화에 대응하지 못해서 오픈 시점부터 바로 진부(陳腐) 해져가는 센터는 설비 즉 하드웨어 중심의 접근 방식이라고 할 수 있습니다.
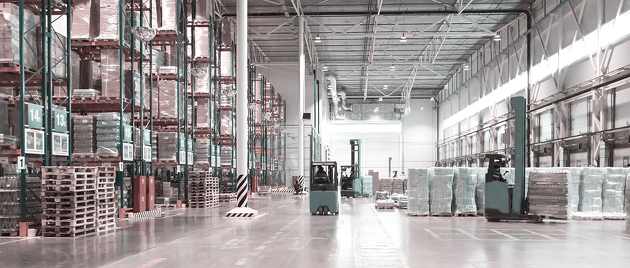
공간, 생산성, 기술의 재정의를 물류센터 구축 전략과 접목해 기술의 변화와 사업 환경 변화에 선도적으로 대응하고 적용 가능한 나날이 진보(進步)해 나가는 소프트웨어 중심의 가치로 전환되어야 지속적인 혁신이 가능할 것입니다.
글 l LG CNS 스마트물류사업담당
