국내 온라인 쇼핑 시장의 폭발적인 성장이 계속되고 있습니다. 통계청 발표에 따르면 국내 온라인 쇼핑 거래액은 2017년 기준 78조 2,000억으로 2005년 10조 6,000억에서 연평균 약 20%의 성장을 보여주고 있습니다.
온라인으로 영역을 넓히고 있는 기존의 오프라인 유통 대기업들과 시장에서 뒤처지지 않으려는 온라인 쇼핑 업체 간의 경쟁도 점점 치열해지고 있는데요. 유통 업체들은 경쟁에서 살아남기 위해 물류 센터의 통합화, 대형화를 통해 물류 비용을 줄이는 데 과감한 투자를 하고 있습니다.
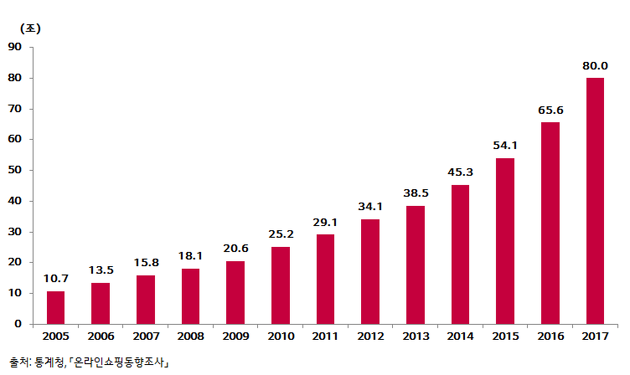
그러나 철저한 계획 없는 물류 센터의 통합 및 대형화는 업체들이 기대한 만큼의 이익을 주지 못할 수 있습니다. 통합 물류 센터의 가장 큰 장점 중 하나는 통합 재고 운용이 가능해져 재고 보관 공간과 기간을 획기적으로 줄일 수 있다는 점입니다.
그러나 그만큼 통합 물류 센터에서 처리해야 하는 주문의 유형이 늘어나게 되어 센터 운영의 복잡도가 매우 증가합니다. 전통적 오프라인 매장 물류보다 B2C(Business to Consumer) 온라인 물류는 필요한 설비가 많아지고, 주문 처리 난이도가 매우 높아, 물류 센터 복잡도를 많이 증가시킵니다. 다음 표는 기존의 매장 물류와 온라인 물류의 차이를 보여줍니다.
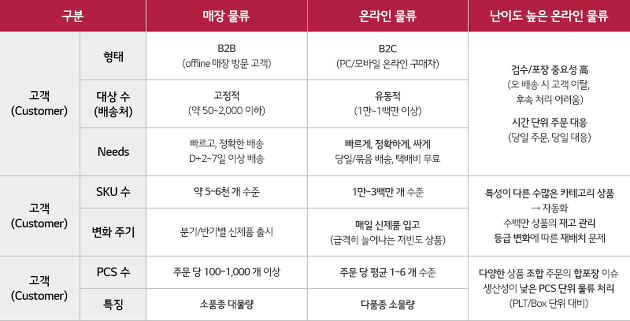
온라인 물류의 증가로 주문 하나에 여러 종류의 SKU(Stock Keeping Unit, 재고 관리 단위)들이 포함된 합포(合浦) 주문이 늘어나고 있습니다.
아래 그림은 일반적인 물류 센터에서 합포 주문을 처리할 때 필요한 업무 구분과 설비를 나타낸 업무 흐름도인데요. 합포 주문은 다양한 자동화 설비와 합포 설비를 필요로 해 물류 센터의 복잡도를 증가시키는 가장 큰 요인이고, 추가적인 이슈를 발생시킵니다.
이런 이슈들은 물류 자동화만으로는 해결할 수 없고, 물류 운영 최적화를 통해 풀어내야 하는데요. 이번 원고에서는 합포 주문의 증가에 따라 발생할 수 있는 물류 센터 내의 이슈들을 소개하고, 이를 해결할 수 있는 최적화 방안을 소개하고자 합니다.

이슈 1. 작업 배치 계획 생성
물류 센터에는 다양한 주문 유형과 설비가 혼재하기 때문에, 설비 별 주문 처리 계획을 세우는 것이 필요합니다. 복잡한 물류 센터에서 다양한 설비들의 용량을 효과적으로 사용할 수 있어야만 하는데요.
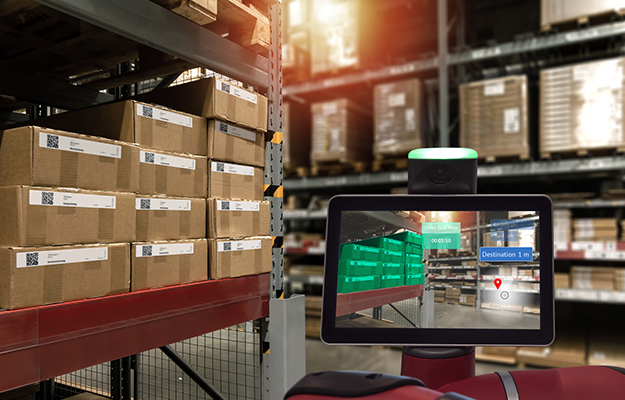
이를 위해서는, 여러 설비에 영향을 주는 주문 유형을 먼저 설비에 할당하고, 남는 설비 용량을 사용해서 처리할 수 있는 주문들을 후 순위로 할당하는 등의 운영 로직이 필요하게 됩니다. 또한, 일일 작업량을 적절한 작업 단위로(Batch) 나눠줄 수 있어야 합니다.
작업 배치 계획 및 설비 별 주문 처리 계획에 대한 운영 로직은 최적화 영역에서 말하는 작업 할당 계획 문제로 모델링 한 결과로 도출할 수 있습니다. 작업 할당 계획 문제는 한정된 자원을 이용해서 주어진 시간에 최대의 작업을 처리하는 작업 계획을 생성하는 문제로, 다양한 설비가 배치된 통합 물류 센터일수록 반드시 해결해야 할 과제입니다.
이슈 2. 보관 설비 형태를 고려한 SKU 보관 위치 결정
물류 자동화가 많이 이루어지면서 자동 창고에 재고를 보관하는 경우가 빠르게 늘어나고 있지만, 아직 사람이 직접 창고에 상품을 보관하고 꺼내오는 수동 창고도 많이 존재하고, 자동 창고와 수동 창고 모두 사용하는 물류 센터도 자주 찾아볼 수 있습니다.
창고의 기능은 같지만, 자동 창고와 수동 창고에서 효율적인 SKU 보관 위치는 서로 다릅니다. 수동 창고에서는 일반적으로 작업자가 필요한 SKU가 어느 구역에 있는지에 대한 정보만 알고, 정확한 위치는 모르기 때문에, 비슷한 종류의 SKU를 같은 장소에 보관할 필요가 있습니다. 비슷한 종류의 SKU는 같이 필요한 경우가 많기 때문인데요.
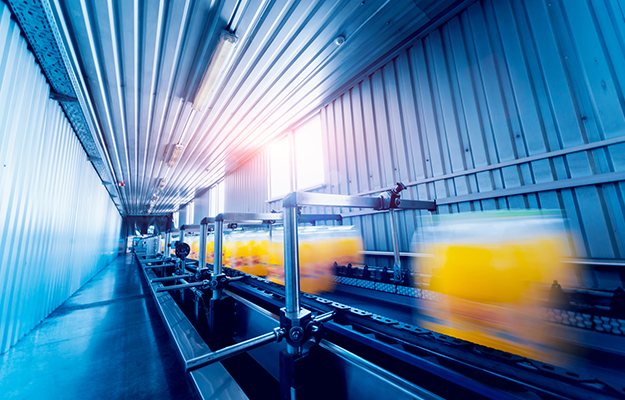
하지만 자동 창고에서는 연관성이 높은 SKU를 분산해 놓는 것이 더욱 효율적일 때가 많습니다. 자동 창고에서는 각 SKU의 정확한 위치가 계속 관리되고 있고, 여러 대의 자동 설비가 동시에 작업할 수 있기 때문에, 설비 간의 업무량 밸런스, 간섭 최소화가 더욱 중요한 관리 지표가 되기 때문입니다.
수동 창고와 자동 창고에 적용할 수 있는 최적화 해법도 달라지는데, 수동 창고는 연관 SKU를 모아주는 Clustering 알고리즘, 자동 창고는 설비 간의 간섭이 존재하는 상황에서 Load balancing 알고리즘 등이 필요합니다.
이슈 3. 보충을 고려한 피킹
합포 설비의 용량을 고려한 총량 피킹 계획 생성이 필요합니다. 총량 피킹이란 주문 단위 별로 피킹 하는 오더 피킹과 달리, 당일 주문 내역을 종합해 SKU 별 총 수량 혹은 큰 묶음 수량 단위로 피킹 하는 것을 말합니다.
예를 들어 100명의 고객이 볼펜과 지우개를 하나씩 구매했다면, 오더 피킹 상황에서는 작업자가 ‘볼펜 1개 ▶ 지우개 1개 ▶ 볼펜 1개 ▶ 지우개 1개’ 이런 식으로 총 200회 피킹 해야 합니다. 하지만, 총량 피킹 상황에서는 볼펜 100개 ▶ 지우개 100개 단 2회만 피킹 하는 것을 말합니다.
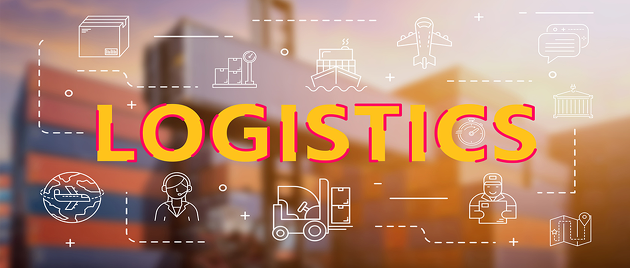
이렇듯, 총량 피킹은 보관 구역에서의 피킹의 효율을 극대화할 수 있는 방법이지만, 합포 설비의 용량에 대한 고민이 같이 필요합니다. 예를 들어, 합포 설비의 용량이 부족해 볼펜 100개를 보충했을 때 가득 찬다면 볼펜과 지우개가 같이 포함된 주문을 피킹 하지 못하게 됩니다.
해결책으로는, 작업 차수를 나눠서 첫 번째 차수에는 볼펜 50개, 지우개 50개만 먼저 총량 피킹 해서, 해당하는 수량만큼의 주문을 차수에 포함하고, 이후 작업 차수에 나머지 볼펜과 지우개가 포함된 주문을 처리하는 방법을 생각해볼 수 있는 것입니다.
이슈 4. 설비 간 이송을 고려한 피킹
총량 피킹을 통해 피킹 한 SKU를 합포 설비로 이송할 때도 효율화를 추구해야 합니다. 일반적으로 총량 피킹 과정에서 합포 설비로 옮길 때 여러 개의 상품을 규격화된 토트에 담아 옮기게 되는데요.
이때 계획 없이 옮기게 되면, 불필요하게 많은 토트를 사용하게 되어 공(空) 토트 관련 업무가 늘어나게 되고, 이송 설비의 부하가 증가하게 됩니다.
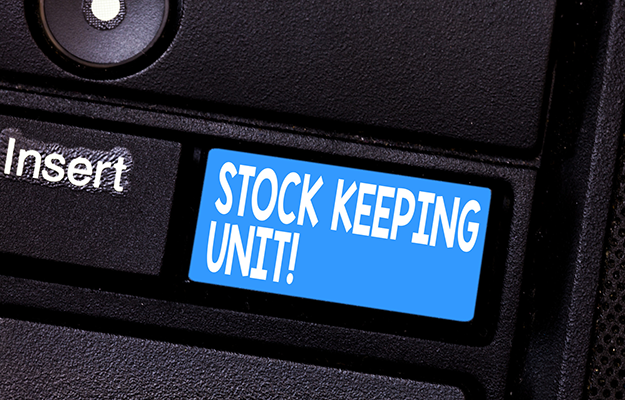
이를 해결하기 위해서는 SKU의 체적 정보와 토트 규격 정보를 활용해, 총량 피킹 작업자가 실행할 수 있는 최적의 토트 적입 계획이 필요합니다. 카토니제이션(Cartonization) 이라고 불리기도 하는 이 과정은 최적화 영역에서 굉장히 많이 다뤄지고 있는 상자 채우기 문제(Bin packing problem)로도 모델링이 가능합니다.
이슈 5. 합포 설비 생산성 최대화를 위한 보충
온라인 쇼핑의 급증으로 합포 설비의 생산성이 물류 센터 전체의 생산성을 좌우하는 경우가 늘고 있습니다. 하지만, 합포 설비의 생산성에 영향을 미치는 두 가지 요소가 상충하기 때문에 면밀한 분석이 필요합니다.
제1요소는 각 작업 공간(Work Station, WS)의 균등한 업무량입니다.
합포 설비의 생산성은 가장 생산성이 떨어지는 특정 WS의 생산성에 의해 결정됩니다. 따라서 사전에 충분한 분석을 거쳐 각 작업 공간에 최대한 균등하게 업무량을 나눠줄 필요가 있습니다.
제2요소는 주문 토트가 거쳐야 하는 WS의 수를 줄이는 것입니다.
주문 토트가 여러 WS에 방문해야 한다면, 합포 설비를 구성하는 이송 설비에 많은 부하가 걸리게 됩니다. 반면에, WS 방문 횟수를 줄이기 위해서는 서로 연관성이 높은 SKU들을 하나의 WS에 집중시켜야 하는데, 이 과정에서 자연스럽게 WS 간에 처리해야 할 업무량의 편차가 발생할 수밖에 없습니다.
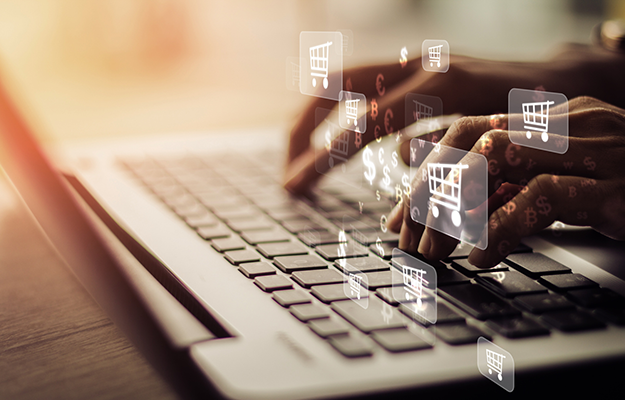
극단적인 예를 들자면, 오직 하나의 WS만 운영한다면 모든 토트의 방문 WS 수는 1로 최소화되지만, 전체 설비의 생산성은 오직 하나의 WS만 존재하는 설비처럼 저하될 것입니다. 따라서, WS 간의 업무량 균등화와 토트 방문 횟수 최소화라는 두 마리 토끼를 모두 잡을 수 있는 고도화된 운영 계획이 뒷받침되어야지만 합포 설비의 생산성을 높일 수 있습니다.
이슈 6. 합포 설비 자원의 효율적인 활용을 위한 보충 및 주문 처리 계획
합포 설비의 효율적인 운영을 위해서는, 합포 설비에 보충될 SKU들의 순서와 그에 따른 주문 처리 순서를 조화롭게 맞춰 나가야 합니다. 앞서 ‘보충을 고려한 피킹’에서 언급했듯, 합포 설비의 용량을 효율적으로 활용할 수 있어야 많은 주문을 효과적으로 처리할 수 있습니다.
아래 그림은 합포 설비에 계획 없이 SKU를 보충하고 주문을 투입할 때, 주문 처리에 실패하게 되는 사례를 보여줍니다. 해당 사례는 간단한 예제이기 때문에, 독자들이 SKU 보충 순서와 주문 처리 순서를 조금씩만 바꿔보면, 주어진 합포 설비로(SKU 저장 Cell 3개) 모든 주문을 처리할 수 있는 계획을 만들어낼 수 있습니다.
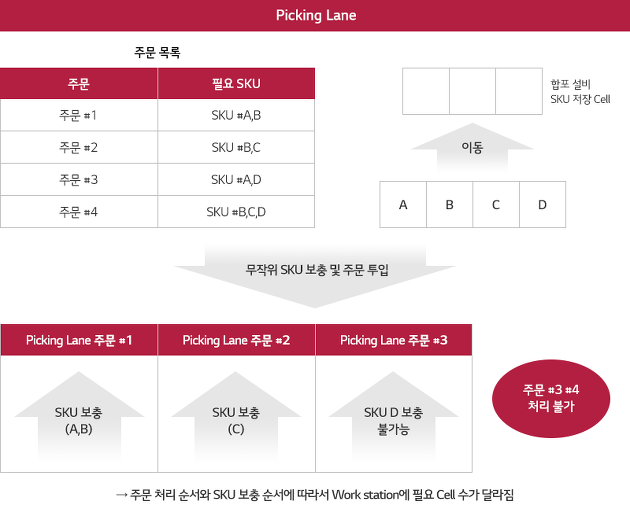
하지만 주문이 몇만 개 단위로 늘어나고, SKU도 1만 개 이상으로 많아진다면 종이와 펜으로 풀기에는 불가능한 문제가 됩니다. 이를 해결할 수 있는 여러 방법 중 하나는, SKU와 주문 간의 연관 관계를 활용한 Clustering 알고리즘을 사용하는 것이고, 상황에 따라 고민해볼 수 있는 다양한 방법이 존재합니다.
이에 더해, 이러한 합포 설비 운영 계획을 역으로 이용하면, 각 물류 센터에 필요한 합포 설비 용량을 계산할 수도 있습니다. 취급하는 SKU 수보다 훨씬 적은 합포 설비의 용량으로도 목표 주문량을 처리할 수 있게 되는 것입니다.
지금까지, 온라인 물류 시장이 성장하면서 발생할 수 있는 물류 센터 내의 다양한 운영 이슈를 살펴보고, 이를 최적화 관점에서 어떻게 모델링하고 해결할 수 있는지를 알아보았습니다.
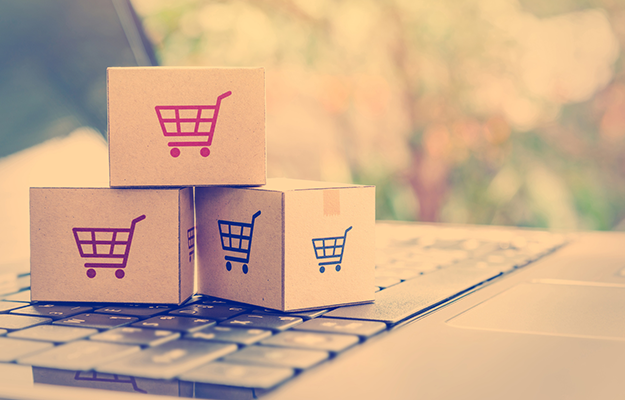
물류 센터는 점점 더 대형화되고, 복잡해질 것이고, 지금보다도 더 다양한 최적 운영 방안이 필요해질 것이기 때문에, 이런 기능들이 포함될 물류 센터 운영 시스템을 구축하는데도 점점 많은 자원이 필요하게 될 것입니다. 따라서, 다양한 물류 센터 환경에서 최적 운영 방안을 적용할 수 있는 범용성이 있는 운영 시스템을 보유한 업체일수록, 많은 고객의 관심을 받을 것이 자명합니다.
범용적인 운영 시스템을 만들기 위해선 기존에 구축한 운영 시스템들을 분석해 공통점을 갖는 영역을 모듈화하는 것이 필수적입니다. 또한, 구축 과정에 참여했던 전문 인력과 고객과의 심화 인터뷰 등을 통해 기존 운영 시스템의 개선점을 찾아내는 과정을 꾸준히 지속해야, 4차 산업혁명 시대에 시장을 선도하는 물류 업체가 될 수 있을 것입니다.
글 l LG CNS 스마트물류사업담당
